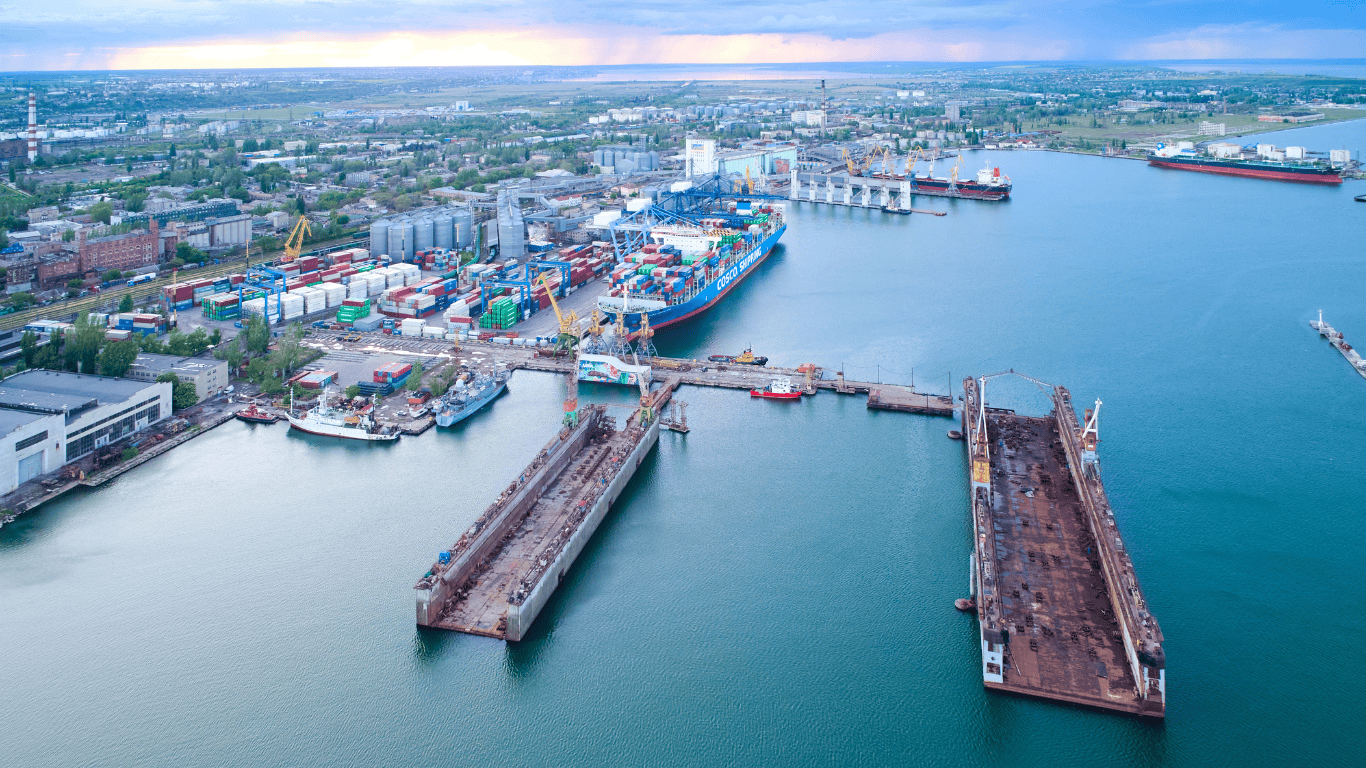
Wencon Epoxy Solutions for the Maritime Industry
With over 40 years of experience, Wencon has delivered top quaity repair and maintenance epoxy solutions within corrosion protection of ship equipment to the maritime industry. Wencon solutions differ from temporary onboard repairs to permanent scheduled maintenance during drydocking.
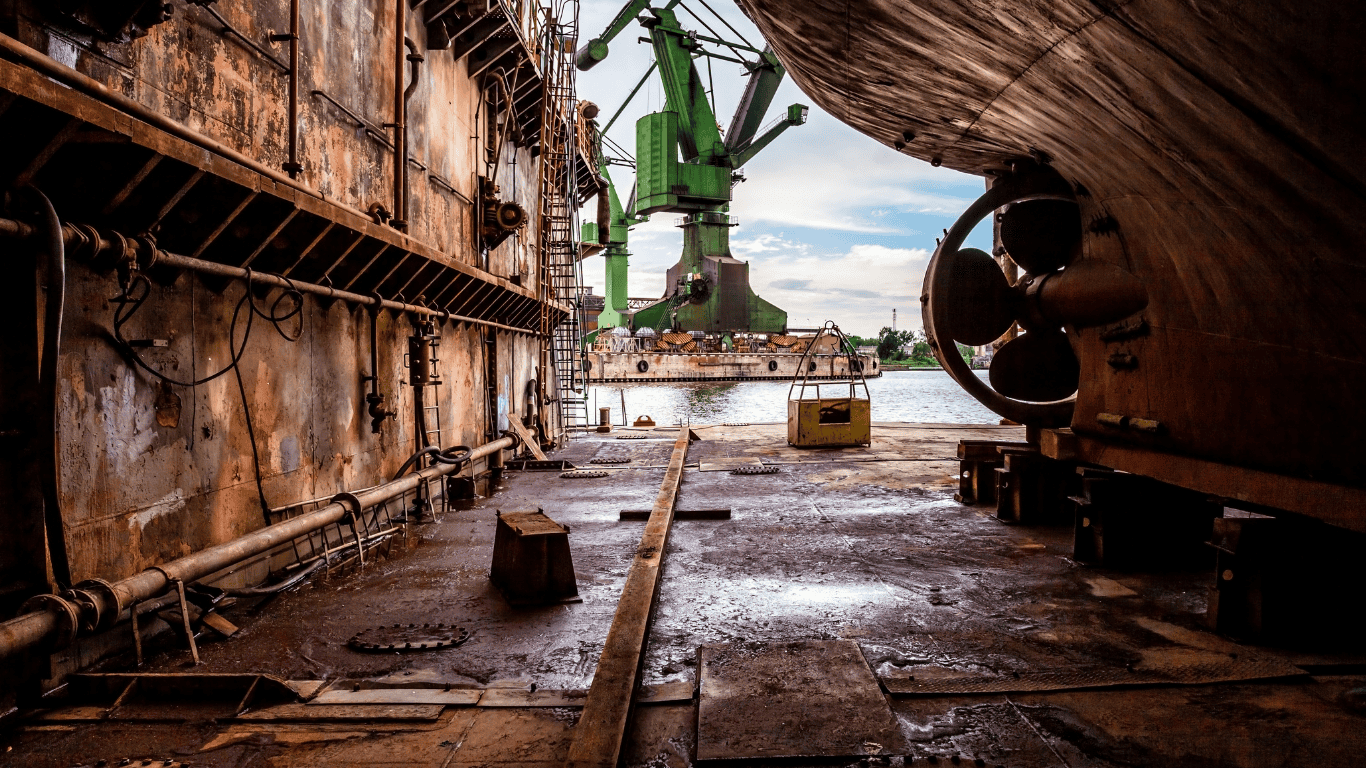
Keep Operating with Wencon
Avoid downtime and keep the vessel running with Wencon epoxy products that protect ship assets against corrosion
Temporary repairs can be done by the crew onboard with Wencon repair kits customed for your needs.
Scheduled permanent repair and maintenance of ship equipment during drydocking with Wencon epoxy coating will save you time and money. You do not have to wait for new assets to arrive and the repair can be done in a few days depending on the case.
Discover Wencon solutions for protection of ship equipment
Explore our interative ship map, where we have located the most common repair and maintenance epoxy solutions. The chosen solutions are an indication of the broad variety of asset repair we provide, but not limited to. If you are searching for another case that is not shown on the interactive ship map, please reach out to us for support and personal guidance.
Reduce scope 3 emissions
In collaboration with Reflow, you can get product assessments that help solve decarbonization challenges in scope 3 and shows how you contribute to a greener maritime industry with actual data.
Our LCA-based models can be used to see the difference between repair vs replace of assets. With our calculations, shipowners get data to support environmental claims, sustainability reporting and green procurement.
Spray application: Reach larger areas fast and effective
Wencon UW Coating LV is a low viscosity coating that can be sprayed on, brushed on, or injected on depending on solution and repair task. The coating can be applied under water and cures on wet surfaces and adheres well to all metal types and GRE material as well.